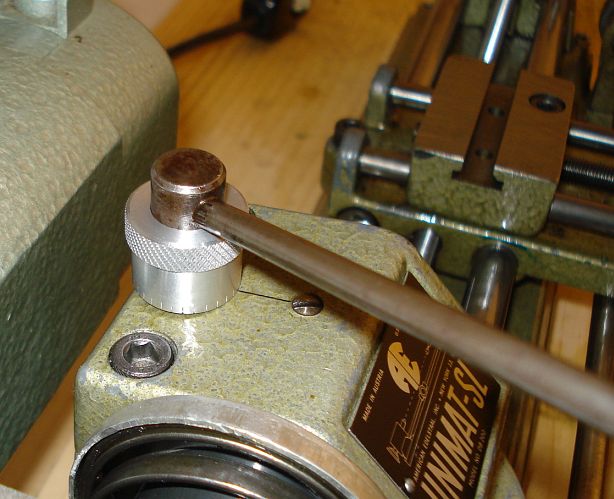
Although
the step of one milimeter per line does not seem too good at first, it
is in fact adequate for most operations. Nevertheless, one could never
expect to achieve the step size of the X and Y axis, because there is
not a fine pitch screw on the Z-axis. However, the milimeter lines are
close enough and the half milimeter can be very comfortably set by
observing the two adjacent lines and halfing their distance. Going to
less than half milimeter is not very practical, considering the
backlash of the lever. In such a case, you can always use an external
precision depth measure gauge.
To finish the gauge, a knurling tool was used to make a diamond pattern
on the aluminum ring and the stainless steel set screw, so that they
can be both set quickly using your fingers, with no need for a tool.